A resin manufacturer installs a chain-drag conveyor to better contain a combustible material.
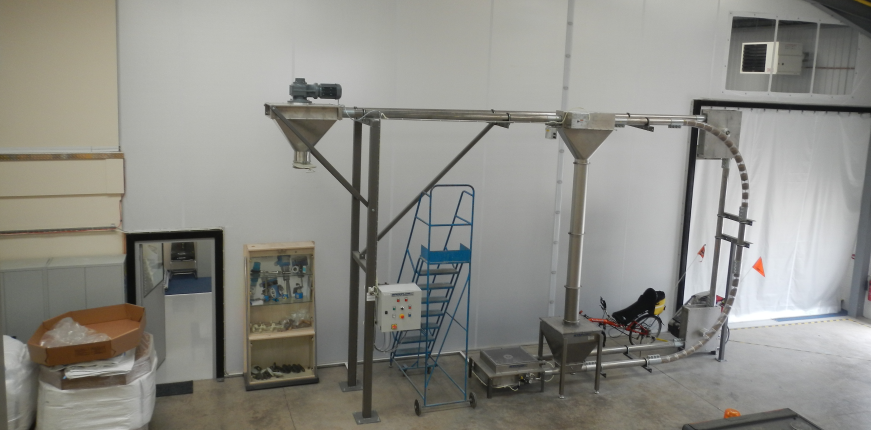
About Hexion
Thermoset resins (resins that set under heat) have an important role in a wide range of industries. Once cured, however, these resins can’t be reprocessed or reshaped without a complete chemical breakdown. As a result, chemicals are frequently added to thermoset resins such as polyester, epoxy, and vinyl ester to render them processable for specific applications. Hexamine, for example, a white crystalline powder made from a reaction between ammonia and formaldehyde, is a chemical additive used primarily as a hardener to create heat-resistant thermoset resins.
Hexion, headquartered in Columbus, Ohio, is a producer of epoxy specialty resins, modifiers, and curing agents. The company produces a range of materials for the paint, packaging, power generation, aerospace, and various other industries. Hexion ‘s plant in Acme, N.C., manufactures hexamine, which is used to create several products. The material is highly combustible in its powdered form and becomes a combustible dust when airborne. J.t can also cause respiratory, eye, and skin irritation and allergic reactions, and the material can release residual formaldehyde gas during processing.
A Hazardous Situation
At Hexion ‘s Acme location, the company had been using two horizontal screw conveyors to convey the material to a dryer in the manufacturing process, but the conveyors were prone to overloading from surges in material flow. If a conveyor became overloaded, the material would force off the conveyor’s cover, resulting in dangerous material spillage and posing a hazard to workers and other plant equipment. Because of the material’s propensity to become airborne, operators had to carefully monitor the screw conveyors to prevent overloading. When overloading did occur, operators often had to stop production until the area was thoroughly cleaned.
A Safer Solution
Hexion decided to search for a new conveying system to help ensure worker safety and equipment reliability. The new system needed to be safer, dust-free, and have no metal to-metal contact that could create sparks and pose an explosion hazard. The company sent a material sample to Spiroflow, a Monroe, N.C.-based powder handling and processing systems supplier with whom Hexion had worked previously. The supplier recommended replacing the screw conveyors with a tubular chain-drag conveyor to prevent material spillage and dust leakage and increase overall plant safety.
“We looked at flexible conveyors and pneumatic conveying but didn’t have the confidence that they would perform as well as the chain-drag conveyor,” says Hexion’s hexamine production leader Joel Johnson. “Drag conveying was a process we wanted to try, and the supplier worked out the special details with us to meet the specific challenges of our material.”
With the new system, a T2 universal bulk bag unloader with a 10-inch diameter material outlet and a rubber dust membrane feeds the material into the new fully enclosed 3-inch diameter chain-drag conveyor. The conveyor is powered by a 1-horsepower motor and has Type 304 stainless steel material contact surfaces and a sealed-pin chain mounted with high-temperature ultra high-molecular-weight polyethylene discs. As the motor pulls the chain, material enters the conveying line and is pushed along the tube by the circular discs to the conveyor’s discharge. A ½-horsepower chain vibrator helps to ensure complete material discharge from the conveyor. Also, the bulk bag unloader allows the material to be recycled in a safer, more dust-free manner.
Because hexamine is an explosive material, the new system is designed without metal-to-metal contact points to eliminate the possibility of sparks, and the conveying line is capable of withstanding the material’s maximum explosion pressure. Also, the steady movement of the conveyor’s chain prevents surges and keeps the material inside the conveying line and out of the work environment.
“Now we don’t worry about material dusting, and this is extremely important,” Johnson says. “Our operators had to carefully watch the old screw conveyors, but our new system just runs. We don’t have to watch or worry about it.”
The lack of dust and material spillage has also reduced housekeeping and maintenance requirements and increased productivity. “The bulk bag unloader and chain-drag conveyor is just what we needed,” Johnson says. “The supplier delivered on all of our requirements, and we drastically reduced our maintenance time.”
Adding On
The chain drag conveyor has been such a success for Hexion that the company is currently in the process of replacing a higher-speed screw conveyor on another line in the plant. “The chain-drag conveyor has lived up to our expectations,” Johnson says. “Now we’re trying to replace older designs with the best available arrangement to meet our process safety requirements. Employee morale is improved when operators see us working hard to ensure the safest work environment
possible.”